Laser cleaning is a powerful technique for removing contaminants without damaging the base material, but how does it affect surface texture? In this article, we’ll explore how laser cleaning impacts surface roughness, what you can expect on different materials, and how it compares to other cleaning methods.
Laser cleaning often results in minimal surface roughness because it targets contaminants with precision without direct contact or abrasion to the surface. However, factors like laser power, pulse duration, and the type of material can influence the final roughness, making it an effective choice for delicate surfaces or those requiring minimal post-treatment.
While laser cleaning offers excellent control over surface texture, specific outcomes depend on the laser settings and the properties of the materials being cleaned.
What is Surface Roughness in Laser Cleaning?
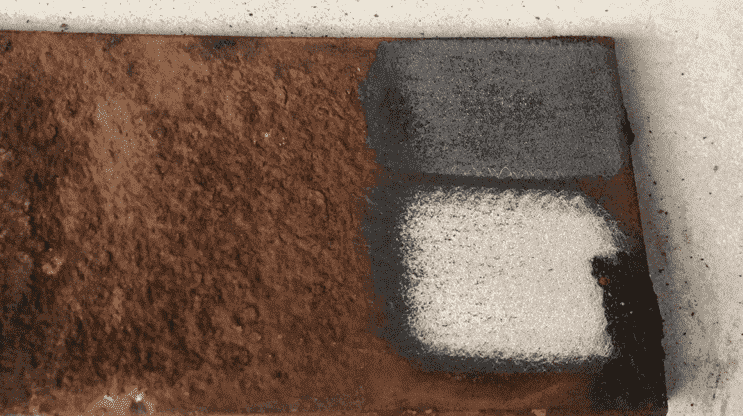
Surface roughness refers to the texture of a material’s surface, characterized by the small irregularities that affect smoothness. In applications like manufacturing, restoration, and maintenance, surface roughness plays a crucial role in performance, appearance, and material longevity.
Laser cleaning, in contrast to abrasive techniques, removes surface contaminants with controlled, high-energy laser pulses that avoid direct contact with the surface. Because of this, laser cleaning can achieve cleanliness with minimal effect on the original roughness, making it a preferred method for delicate surfaces or applications requiring uniform textures.
How Does Laser Cleaning Affect Different Materials?
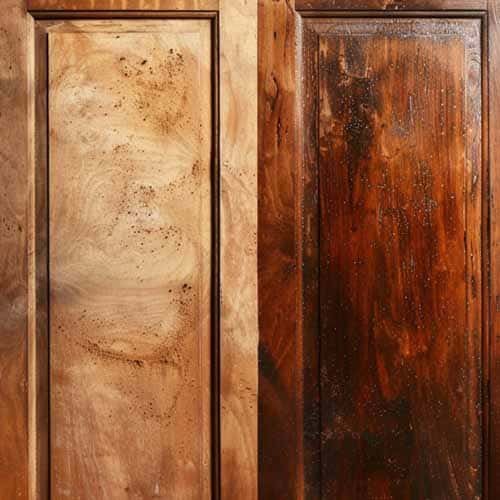
The effects of laser cleaning on surface roughness vary significantly across different materials. Here’s a look at some common types:
- Metals: Laser cleaning is popular for metals like steel, aluminum, and titanium. Metals typically respond well to laser cleaning due to their high thermal conductivity, which helps disperse laser energy efficiently. For metals, laser cleaning often results in smooth, clean surfaces with little to no increase in roughness, provided the correct laser settings are used.
- Non-Metals (e.g., stone, glass, plastics): Non-metallic surfaces react differently to laser cleaning due to lower thermal conductivity. Stone and glass, for example, may experience minor increases in roughness, especially if high-power lasers are used, leading to micro-cracking or slight texturing. Plastics, which are more heat-sensitive, can require lower power and faster pulses to avoid surface melting, which can alter roughness.
Overall, laser cleaning adapts well to diverse materials, though optimal settings should be tailored to each material to achieve minimal roughness.
What Are the Main Factors That Influence Surface Roughness After Laser Cleaning?
Surface roughness after laser cleaning is influenced by various factors, primarily the laser parameters, cleaning environment, and the initial surface condition.
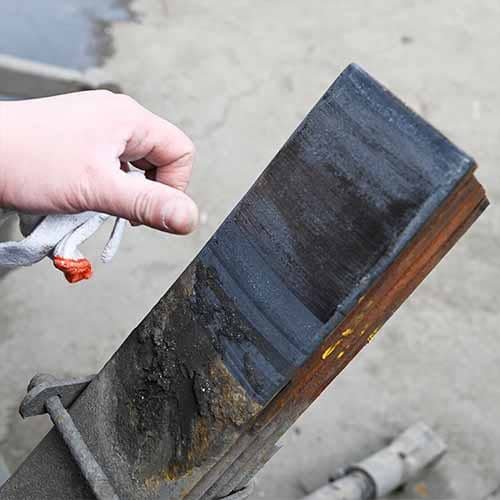
- Laser Parameters: The power, wavelength, pulse duration, and frequency of the laser are critical. Higher power and longer pulse duration can increase the chance of surface alteration, particularly with sensitive materials. Low-power lasers with shorter pulses are better suited for preserving smoothness on delicate surfaces.
- Cleaning Environment: The environment can influence the cleaning effectiveness and surface texture. Conditions like temperature and humidity affect how materials respond to laser energy and can sometimes cause slight variances in roughness levels, particularly in materials sensitive to thermal effects.
- Initial Surface Condition: The initial state of the surface, such as the extent of oxidation or contamination, plays a role in the final roughness. Heavily oxidized surfaces may experience slight roughening as layers of corrosion are removed, exposing a clean but naturally textured surface beneath.
How Does Surface Roughness After Laser Cleaning Compare to Other Methods?
Laser cleaning is distinct from other cleaning methods in terms of how it affects surface roughness. Here’s how it stacks up against some popular alternatives:
- Abrasive Cleaning: Techniques like sandblasting physically remove surface contaminants, which can increase roughness and alter surface characteristics. In contrast, laser cleaning achieves cleanliness without contact, preserving the original surface texture in most cases.
- Chemical Cleaning: Chemical cleaners can dissolve contaminants effectively but may cause surface roughness changes depending on chemical reactions. For example, acids can etch certain surfaces, while laser cleaning avoids such chemical alterations.
- Ultrasonic Cleaning: While ultrasonic cleaning also avoids physical abrasion, it may not be as effective for thicker or bonded contaminants. Laser cleaning offers better control over roughness while effectively removing stubborn debris.
Laser cleaning, therefore, presents a balanced solution, providing the non-contact benefits of ultrasonic cleaning and the effectiveness of abrasive methods without the associated roughness increase.
Is Laser Cleaning Suitable for Delicate Surfaces?
Yes, laser cleaning is highly suitable for delicate surfaces, especially when precision settings are used to maintain minimal roughness. Industries that require careful control of surface texture, such as aerospace, electronics, and heritage conservation, benefit greatly from laser cleaning.
For instance, in aerospace, laser cleaning is employed to remove coatings or corrosion on delicate parts without altering the base material’s smoothness, which is essential for optimal aerodynamic performance. In conservation, laser cleaning removes oxidation and organic materials from historical artifacts without damaging the artifact itself, preserving its original texture.
How Do Laser Cleaning Settings Impact Roughness Levels?
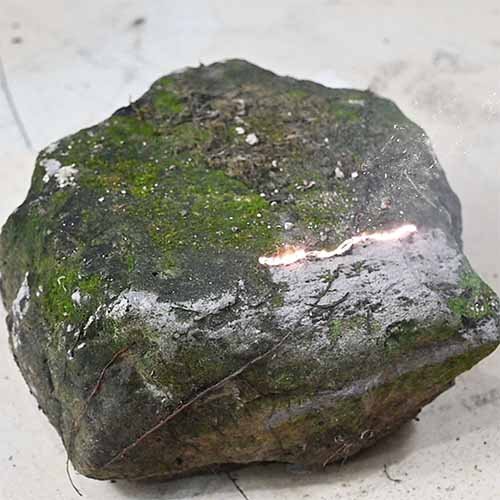
Laser cleaning offers a range of adjustable settings that directly impact surface roughness:
- Power Levels: Higher power settings increase the likelihood of slight roughness due to the depth of material removal. Lower settings, on the other hand, are ideal for minimal roughness but may require more passes to achieve cleanliness.
- Pulse Duration and Frequency: Shorter pulse durations with high frequencies typically result in smoother surfaces, as the laser energy is distributed more evenly. Longer pulse durations can lead to localized heating, increasing roughness, especially on sensitive materials.
To achieve desired roughness levels, operators can experiment with these settings, adjusting them based on the material properties and roughness requirements.
What Research Says About Surface Roughness and Laser Cleaning Efficiency
Studies on laser cleaning and surface roughness have highlighted the effectiveness of this method across various applications. Research has shown that, with optimized settings, laser cleaning can achieve surface finishes comparable to untreated surfaces, particularly on metals. For example:
- Metal Surface Studies: Research on metals like steel and aluminum indicates that laser cleaning can remove rust and oxidation without increasing surface roughness significantly, allowing for immediate post-processing like coating or welding.
- Non-Metallic Surfaces: Studies have observed that stone and glass exhibit minor roughness changes under laser cleaning, but these can be minimized with low-power lasers and controlled pulse durations.
Overall, these findings support the idea that laser cleaning is a versatile, precise option for applications requiring controlled roughness and high cleaning efficiency.
Summary: When to Use Laser Cleaning for Optimal Surface Roughness
Laser cleaning is an ideal choice for preserving surface texture while achieving thorough cleanliness, especially on materials like metals that require minimal post-treatment. By adjusting settings like power, pulse duration, and frequency, laser cleaning can meet diverse application needs, from delicate aerospace components to historic artifacts. For applications where surface roughness must be tightly controlled, laser cleaning offers an efficient, non-contact solution that other methods may not match.